生産計画はなぜ難しいのか?IoTが切り拓く改善への第一歩
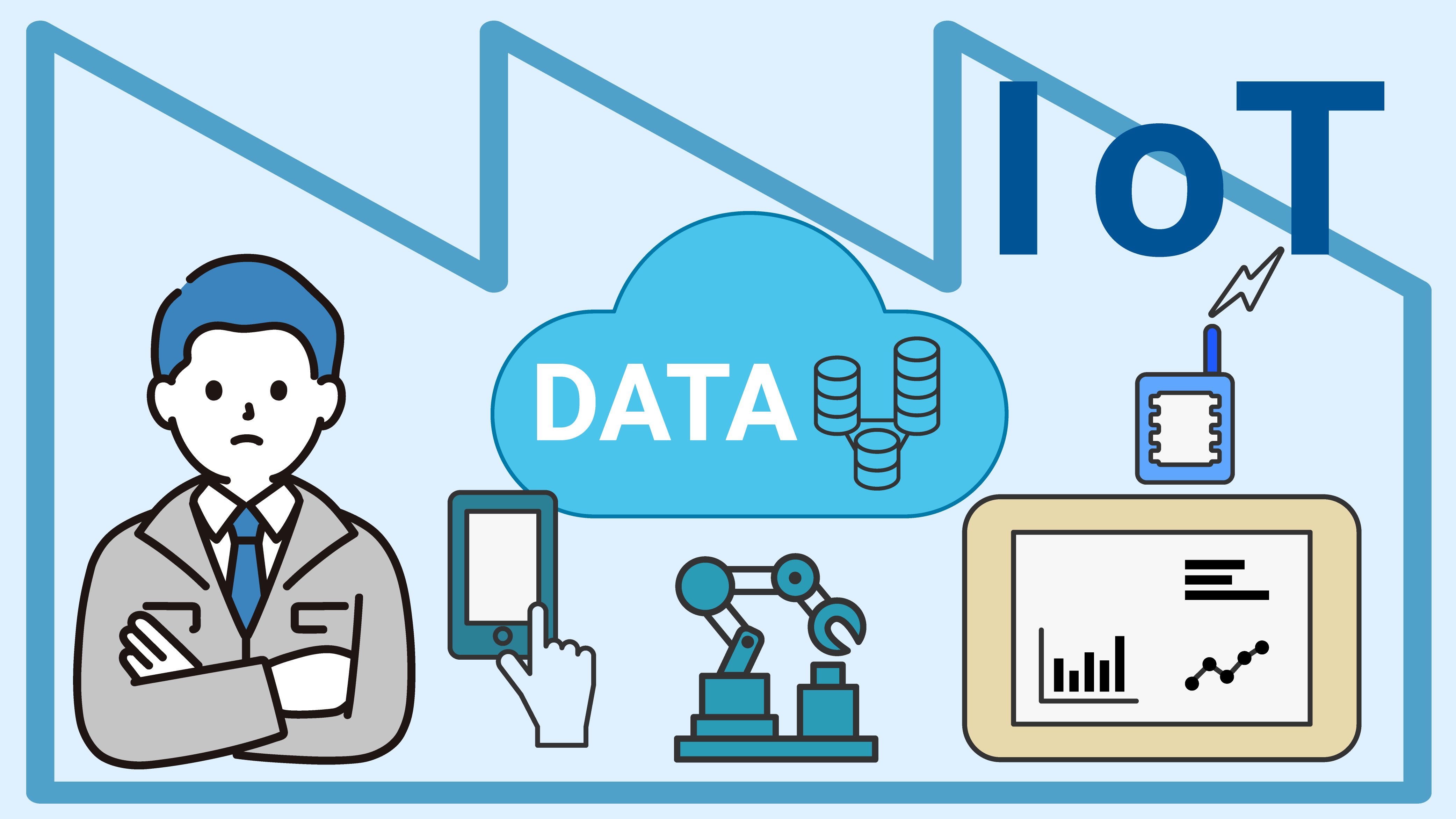
「うちの会社は、ろくに生産計画すら立てられない(計画を立てても守れない)。だから、IoTを導入するには早すぎるのかもしれない。」
こう語る工場経営者がいます。しかし、これは大きな誤解です。生産計画は、そもそも簡単に守れるようなものではありません。むしろ、生産計画が難しいからこそ、IoTが必要なのです。
1. 生産計画が元来難しい理由
生産計画を立てても、その通りに進めるのは極めて困難です。なぜなら、製造現場では多くの不確実な要素が絡み合っているからです。
品質不良、設備の故障、材料の供給遅延、外注工程の遅れ、顧客の急な納期変更など、計画を狂わせる要因は多岐にわたります。さらに、天候による影響や人員の急な欠勤、作業者の熟練度の違い、作業ミスの発生など、複雑な変数が日常的に影響を与えています。
2. それでも生産計画は不可欠
とはいえ、生産計画なくして効率的な製造現場を実現することは不可能です。計画が曖昧であれば、リソースの無駄や納期遅延が常態化し、競争力を失うことは明らかです。だからこそ、生産計画をより良くするための努力は不可欠です。
生産計画は、現場の生産性だけでなく、在庫管理や人員配置、設備稼働率の最適化にも密接に関係しています。適切な計画が立てられていれば、無駄なコストの削減や納期遵守率の向上といった成果も期待できます。
3. 実績に基づく計画の重要性
もし見積工数ベースで生産計画を立てている工場があれば、それはすぐに見直すべきです。過去の実績データを基に計画を組むことで、現実に即したスケジューリングが可能になります。
「うちは実績を元に計画を立てている」と考える管理者も多いでしょう。しかし、その実績は現場の実態を正確に反映しているでしょうか?
作業日報に記録された工数は、作業者の記憶や主観に依存しており、往々にして曖昧さや誤差が含まれます。また、作業者の勤務時間を基に作業時間が割り振られていることがあり、製品に掛かった工数を正しく反映できていない場合もあります。ここで役立つのがIoTです。 IoTなら、人の手を介さずに正確なデータを自動で収集できます。これが、計画精度向上への第一歩となるのです。
4. バラつきへの対応が次の課題
しかし、実績データを基に生産計画を立てても、「計画と実績が合わない」という問題は再び生じることになるでしょう。それは、同じ作業者が同じ製品を加工しても、作業時間にバラつきが生じるからです。異なる作業者が担当すれば、なおさらバラつきは大きくなります。
ここでもIoTは大きな力を発揮します。IoTによって、作業のバラつきの存在とその程度を可視化できます。そして、そのデータを分析することで、バラつきを引き起こす要因を特定し、バラつきを減らすための具体的な改善策を講じることが可能になります。
まとめ
もちろん、これだけで生産計画が完璧に機能するわけではありません。依然として、予測不可能なトラブルや外的要因は発生します。しかし、まずは自社の工数を正しく把握し、それを生産計画に反映させることが重要な第一歩です。
この第一歩を踏み出すことで、次に作業工数のバラつきやその要因が可視化されます。その結果、バラつきを最小限に抑えるための具体的な改善策を立てることが可能となり、生産計画の精度向上につながります。このプロセスを継続することで、計画と実績のギャップを縮小し、より安定した生産体制の構築に寄与するのが、IoTの力なのです。
サービス詳細
➡ 稼働監視キットPro サービス詳細はこちら