稼働監視キットPro 導入インタビュー
「現場の感覚」から「数値に基づく改善」へ
グループで支え合い、工場が変わった
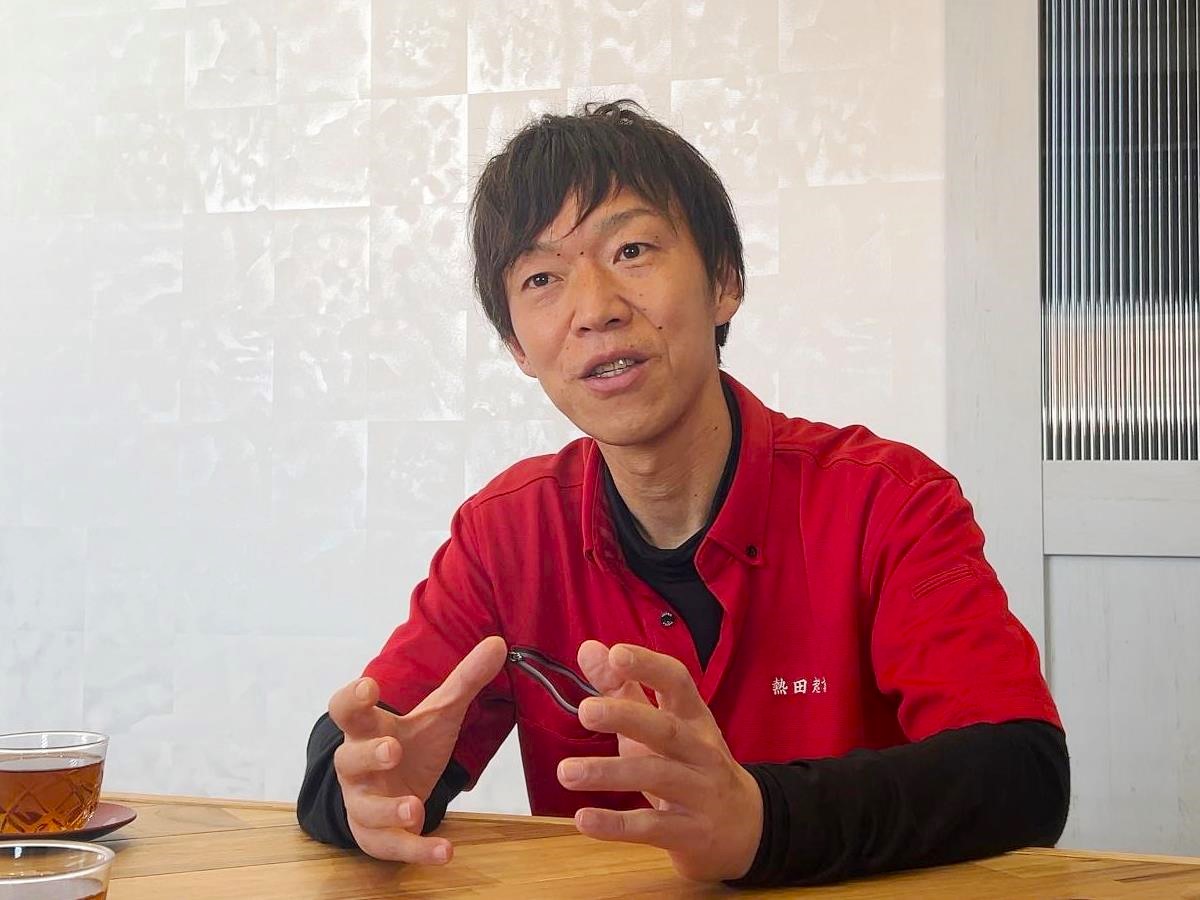
熱田起業株式会社 工場長 西川 篤志 様
航空宇宙部品メーカー
従業員数:36名
導入機能:機械稼働データ収集(8台)、作業者位置データ収集(8人、10箇所)
——「稼働監視キットPro」導入のきっかけを教えてください。
導入のきっかけは、「あいまいな現場」への危機感でした。
以前の現場は、仕事が来たら誰かに割り振り、その人が終わらせてくれるのを待つだけ。基準は「仕事ができる人かどうか」。数値的な裏づけのない属人的な運用に頼っていたのです。
私たちのような金属加工の現場で、生産性を上げるには「機械が動いている間に、人がどのように動くか」が重要です。つまり、機械が止まっている時間を減らすためには、次の段取りや準備をどれだけ効率的に行えるかがカギになります。
その追求には、機械の稼働データだけでなく、人の動き=作業者の位置情報が必要不可欠だと考えました。稼働監視キットPro(工場診断オンライン)は、その課題に対する最適な解決策でした。
——導入にあたって、不安やハードルはありましたか?
もちろん、人は本能的に「現状維持」を好みますので、新しいものを導入する前には、不安や戸惑いの声もありました。しかし、実際に稼働監視キットProを導入してみると、実質的な負担がないことが分かり、特に不満の声は上がりませんでした。
私たちは、「稼働時間を伸ばす」ことを作業者に求めるのではなく、「停止時間を減らすために、管理者がサポートする」という姿勢を貫きました。データを見てみると、作業者は想像以上に多くの雑務を抱えていることが分かりました。そこで、その雑務を減らすための改善に取り組みました。
また、評価の対象も個人ではなくグループ単位としました。グループで成果を上げることを目標にすることで、メンバー間での協力体制が自然に生まれました。たとえば、雑務が一人に集中しないように、グループ内で作業を分担し、稼働停止を最小限に抑える努力が行われるようになったのです。
——現在の活用方法について教えてください。
管理職だけでなく、現場のグループ単位でもデータを活用しています。
半年に一度、各グループがデータをもとに目標を設定し、毎月、その進捗を報告。課題があれば、原因分析と対策の発表も行います。数字に基づく改善サイクルが、現場でしっかり根付いてきました。
さらに、作業単価を可視化する仕組みをつくり、作業者が自分の業務に対して金銭的な意識を持てるようにしています。経営感覚が自然と養われる仕組みです。
——導入して、どのような効果がありましたか?
もっとも大きな効果は、稼働監視キットProを導入してから、売上が2倍になったことです。
これは単に生産量が増えたからではありません。稼働効率が上がり、こなせる仕事量が増えたことで余裕時間が生まれ、その時間を使って現場のスキルアップに取り組むことができたのです。
結果、より高単価・高品質な案件を受注できるようになり、会社全体としての生産性と付加価値が大きく向上しました。単なる数字の可視化ではなく、組織の底力が上がったと感じています。
——今後の展望をお聞かせください。
10年前、受注管理システムを導入した際にも「紙で十分では?」という声がありましたが、いまや電子化によって大幅な効率化が実現しています。
IoTも同じです。最初は「本当に必要か?」という声もありましたが、今では製造現場の分析が飛躍的に進み、大きな変革を達成できたと実感しています。
テクノロジーの進化に背を向けるのではなく、一歩先んじて取り入れる勇気が、次の成長を生むと考えています。
今後、私たちのような多品種少量生産の現場においても、ロボットの活用はますます進むでしょう。そのときに、いま蓄積している人と機械のデータが大きな武器になります。
受注管理システムの時と同様、「もっと早くやっておけばよかった」と思う未来にならないよう、今から手を打つことの大切さを強く感じています。